
Taking Your Business to
the Next Level
Industries
Logistics management is a pivotal function in day-to-day operations of many businesses. While retail and eCommerce face disruption after disruption and keep coming out on top, 50 percent of trucks travel empty on their return journey and warehouses are either overfilled or standing idle.
Digitalization will allow warehousing and transportation operations to elevate customer experience, deliver more value to partners, and consequently – create an effective ecosystem of supply chain providers: manufacturers, carriers, and more.
Digitalization often boils down to two approaches: automation and using data. In this article, we describe how logistics management systems (or LMSs) can bring value by automating processes and using data to make informed decisions.


Services
Typically, logistics works in two directions – forward and reverse. When we talk about logistics, we usually mean forward direction, which includes such operations as receiving and processing an order, checking and preparing inventory, packing and picking an item, dispatching it and selecting a transportation route that will deliver the product to a customer as quickly and efficiently as possible. Reverse direction means any operations with managing incorrect or damaged shipments, repairing items, and reusing or recycling.

Order Management
Receiving and processing an order online usually includes operations of creating and editing inventory, managing customer service, accepting payments, checking for fraud, and handling documentation between manufacturers, suppliers, warehousing, and transportation companies.
To manage orders effectively and avoid double handling errors, orders, inventory, supplier and customer data must be synchronized in one system. Order management software (OMS) receives orders from all your sales channels and monitors them from the moment they’re placed until the customer confirms delivery. This is your main connectivity hub where all information about the order is displayed: routes, location, inventory, warehouse connectivity, and integration with accounting to create invoices and accept payments, etc.
​
​
​
​

Picking
Synced with a scanning device, the software helps pinpoint items throughout the warehouse building. Tracking the barcodes assigned to items, WMS guides the order assemblers to the needed products through the optimized picking route. To ensure the correct lot is selected, pickers doublecheck it: on scanning the attached barcode, the system verifies it. In terms of velocity, batch picking function can be a real timesaver, as it allows for picking many orders in a single run.

Order Tracking
To gain full visibility into product movements, clients are provided with access to an online portal that monitors shipment on the road, alerting to any transit exceptions or unforeseen delays.
​
Usually, location tracking involves subsequent reports in a real-time, vehicle-position database. Another package tracking method is to report the arrival or departure of the object and record the object identification, the location where observed, the time, and the status.
​
Not only vendors but certainly customers need insight into the progress of delivery. Provided with an order ID, they can track the progress of the goods in a corresponding application.
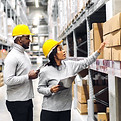
Inventory management
Inventory management is a vital part of the supply chain responsible for controlling and documenting the amount of product for sale. Receiving, storing, and tracking inventory, while dealing with its rapid and constant changes, requires highly accurate product information management. So, automating from classic spreadsheets to inventory management systems (IMS) delivers the needed clarity centralizing all the data in a single location through an inventory management system.
​
​

Warehouse management
Warehouse management is a set of processes maintaining, controlling, and automating warehouse operations. This includes receiving items, moving them, managing warehouse staff using KPIs, maintaining safe work conditions, and using software and hardware to locate and track items.
​
A warehouse management system consists of tools that streamline the workflow of managing goods from arrival at the warehouse through storage and tracking within the location to order management and dispatching further.

Packing
Orders can have specific packaging requirements to guarantee safe shipping or improve the unboxing experience. The WMS helps make sure the packing is performed in the correct order, and as efficiently as possible, according to the rules set by the business.

Connecting to
the carrier network
Logistics management software connects shippers with carriers providing visibility to all concerned to find the best shipping option. To decide on the cheapest carrier, there’re transportation procurement tools. These tools assist in customizing a client’s request for proposal, responding to queries, taking in proposals, and evaluating bids.

Labor Management
Supervising the human side of warehouse operations entails the use of a labor management system integrated into WMS. First, the system assigns tasks to individual warehouse workers using workforce planning and scheduling capabilities. This allows you to track productivity, identify underperforming shifts or workers. The task history environment shows employees’ entire history of activities that can be used for analyzing peak labor, optimizing workflow, and finding solutions where obstacles come into play. In the long run, it will increase productivity and efficiency while lowering labor costs.
​
​
​

Delivery management and scheduling
Supervising the human side of warehouse operations entails the use of a labor management system integrated into WMS. First, the system assigns tasks to individual warehouse workers using workforce planning and scheduling capabilities. This allows you to track productivity, identify underperforming shifts or workers. The task history environment shows employees’ entire history of activities that can be used for analyzing peak labor, optimizing workflow, and finding solutions where obstacles come into play. In the long run, it will increase productivity and efficiency while lowering labor costs.
​
​
​
Career
Join Bleu Logistics
At the Bleu Logistics, you are not just an employee. You are a member of an agency that has Integrity & Honesty, Transparency, and Quality. We help each other grow within our roles — and beyond them.
To accomplish our mission, we seek individuals who will go the extra mile, who do the right and ethical thing every time, and who value and appreciate everyone they meet. This is reflected in the core values that guide our efforts and shape the way we work with customers and each other.
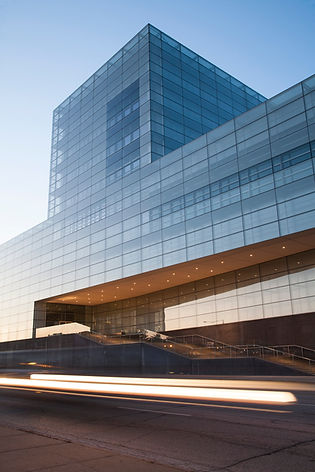

